For generations, block printing has been a lively cornerstone of Indian fashion, transforming fabric with hand-stamped designs crafted from intricately carved wooden blocks. To celebrate The Great Elephant Migration, we’ve teamed up with the finest Indian artisans to bring a touch of Indian excellence to the collection. Explore this ancient craft, our new designs, and the talented artisans behind it all…
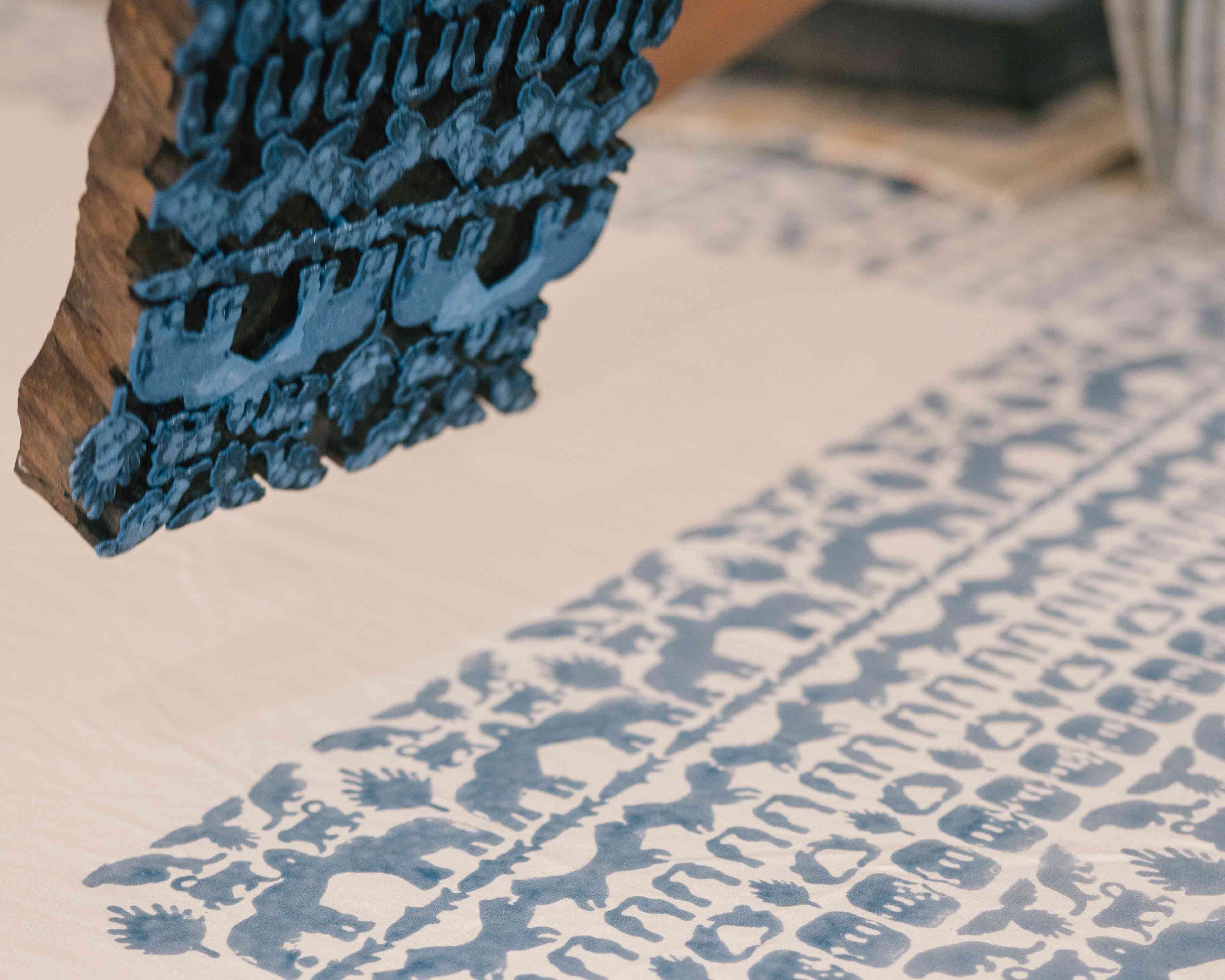
What Is the Block Printing Method?
In a nutshell, block printing is a printing technique that involves pressing and stamping fabric with intricately carved wooden blocks filled with colourful dyes. But, this incredible heritage craft is, of course, more than just pressing blocks onto fabric. There are many complex steps involved from designing and carving each wooden block, to preparing the fabric and mixing dyes to get the most vibrant of colours. Though it’s labour-intensive and requires a huge amount of time and skill, Indian block printing truly is craftsmanship at its finest.
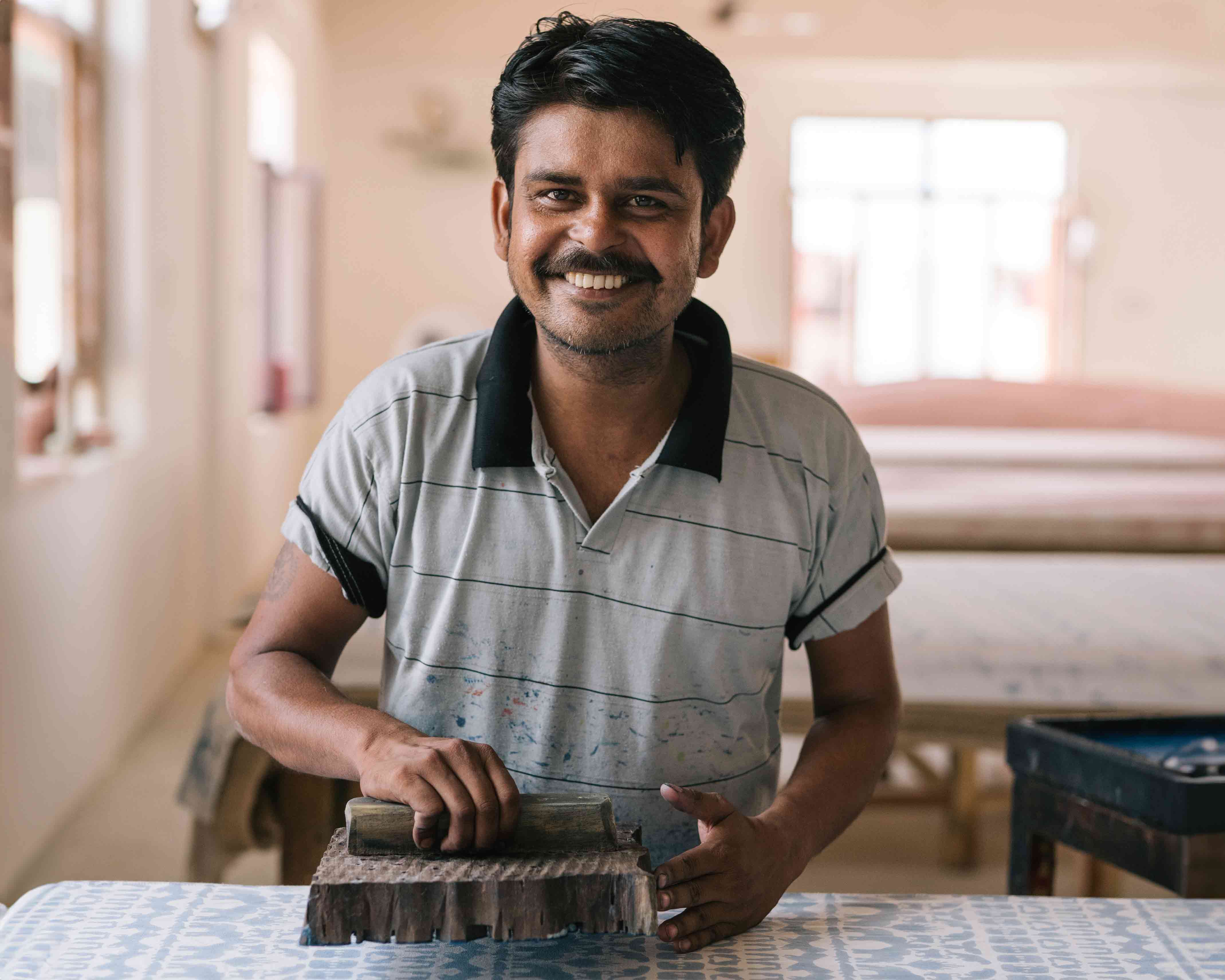
A Sustainable Art
This age-old technique is as intricate as it is impressive, passed down through generations for hundreds of years and not only that but it’s an incredibly sustainable alternative. The block printing process produces minimal waste, uses natural dyes, and uses less water and energy than other methods. We also only use sustainable natural cotton, hemp and linen in our clothing and accessories.
A Journey Into Block Printing
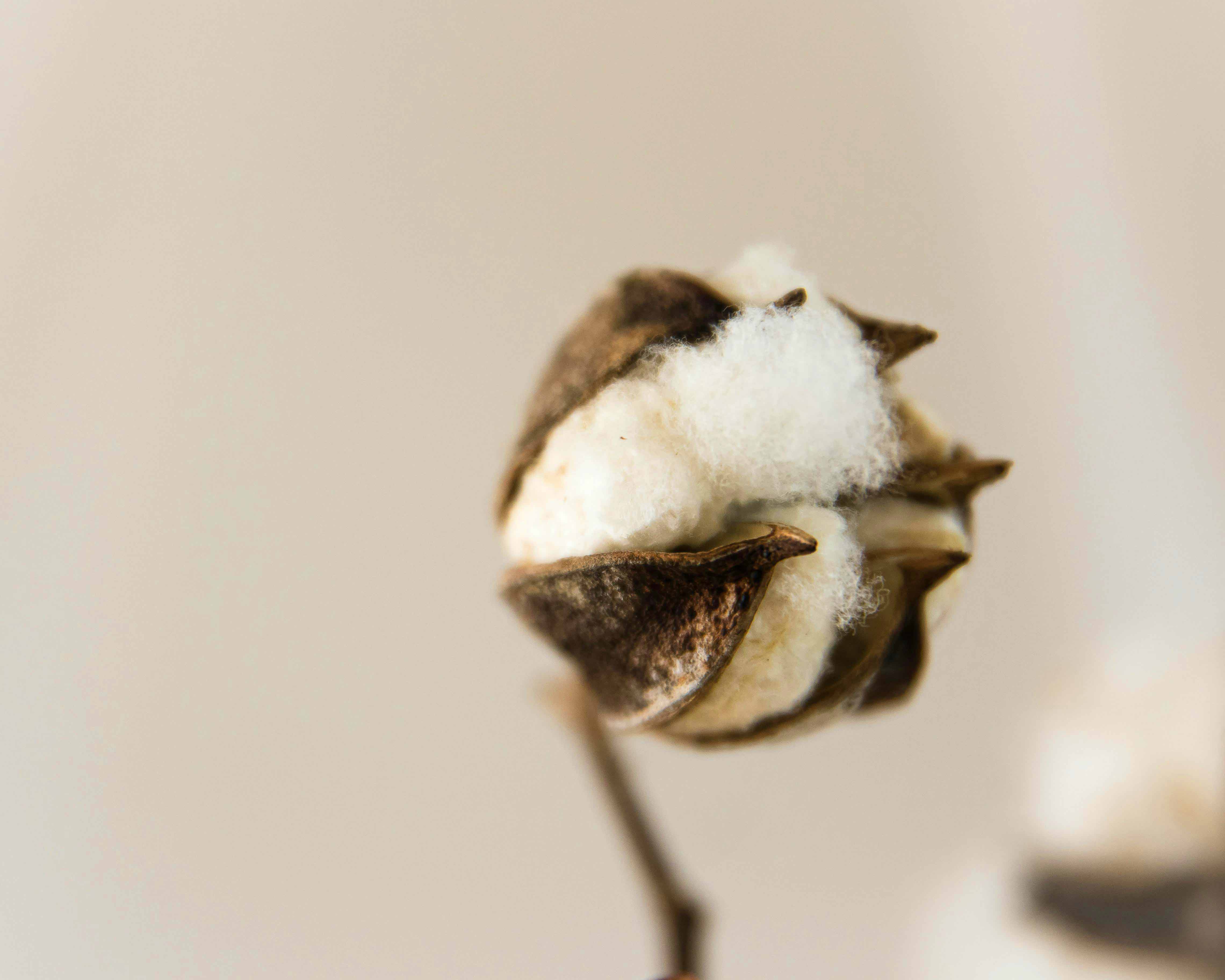
Step 1
The journey of crafting one of our block printed cotton pieces starts with gently hand-picking cotton balls from our fields. The cotton balls are then lovingly laid out to dry naturally under the sun’s rays.
Step 2
Next up, it's time to transform our raw materials into usable yarn. This process is known as carding. It involves delicately separating each cotton fibre by dividing and redividing them until they all align in the same direction and blend together to create our all-important yarn.
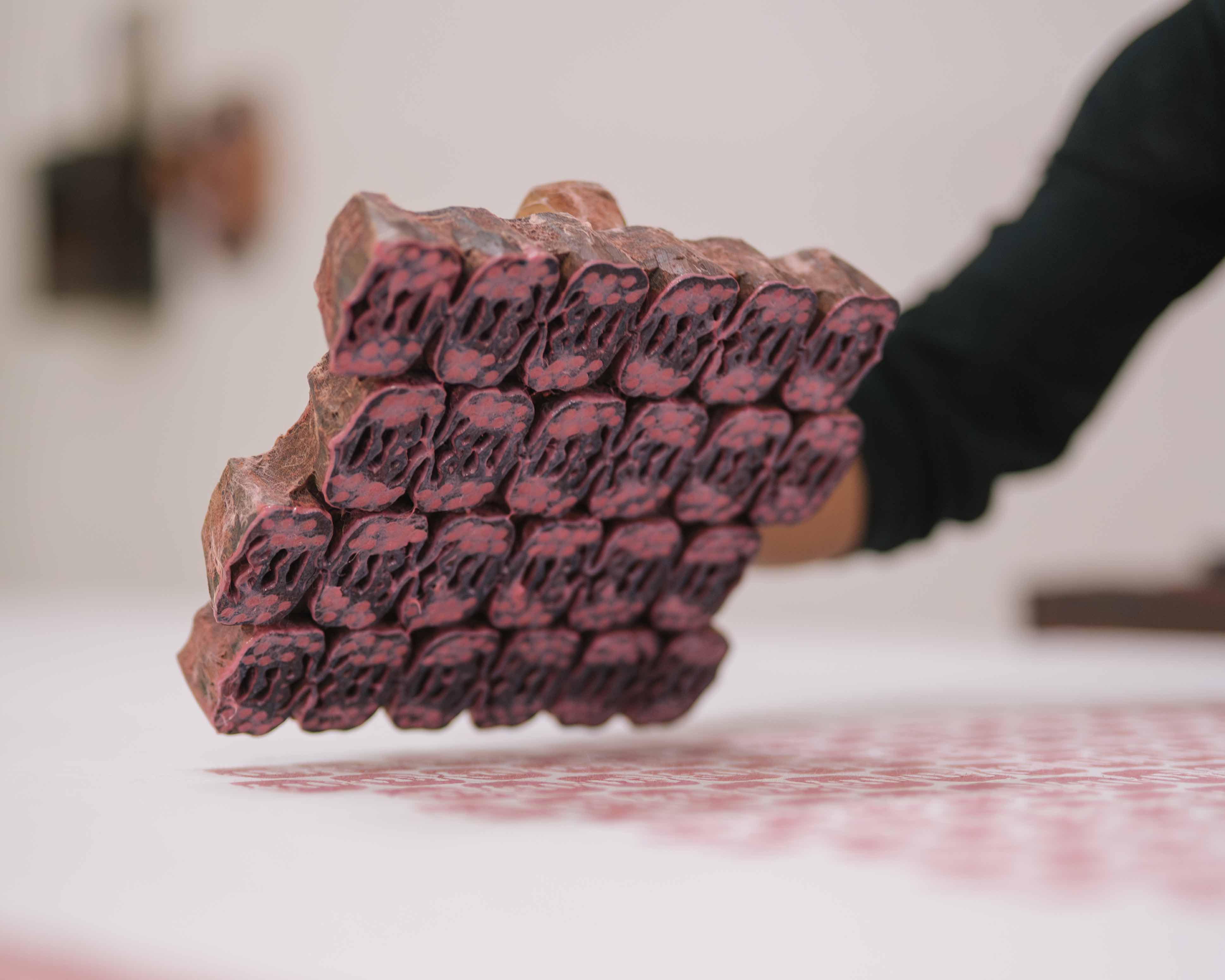
Step 3
The yarn is then skillfully woven into cloth. This involves two sets of yarns being intertwined at right angles to form a fabric. The fabric then undergoes meticulous quality checks to ensure it's of the highest standard.
Step 4
Now it's time for the block carving. Love Brand & Co. founder Oliver Tomalin designs the prints and shows them to our incredible artisans. The artisans then draw and intricately carve the design into wooden blocks. The process of block printing is a tedious one with the blocks themselves taking 2 weeks to be perfected, but the payoff makes it all worthwhile.
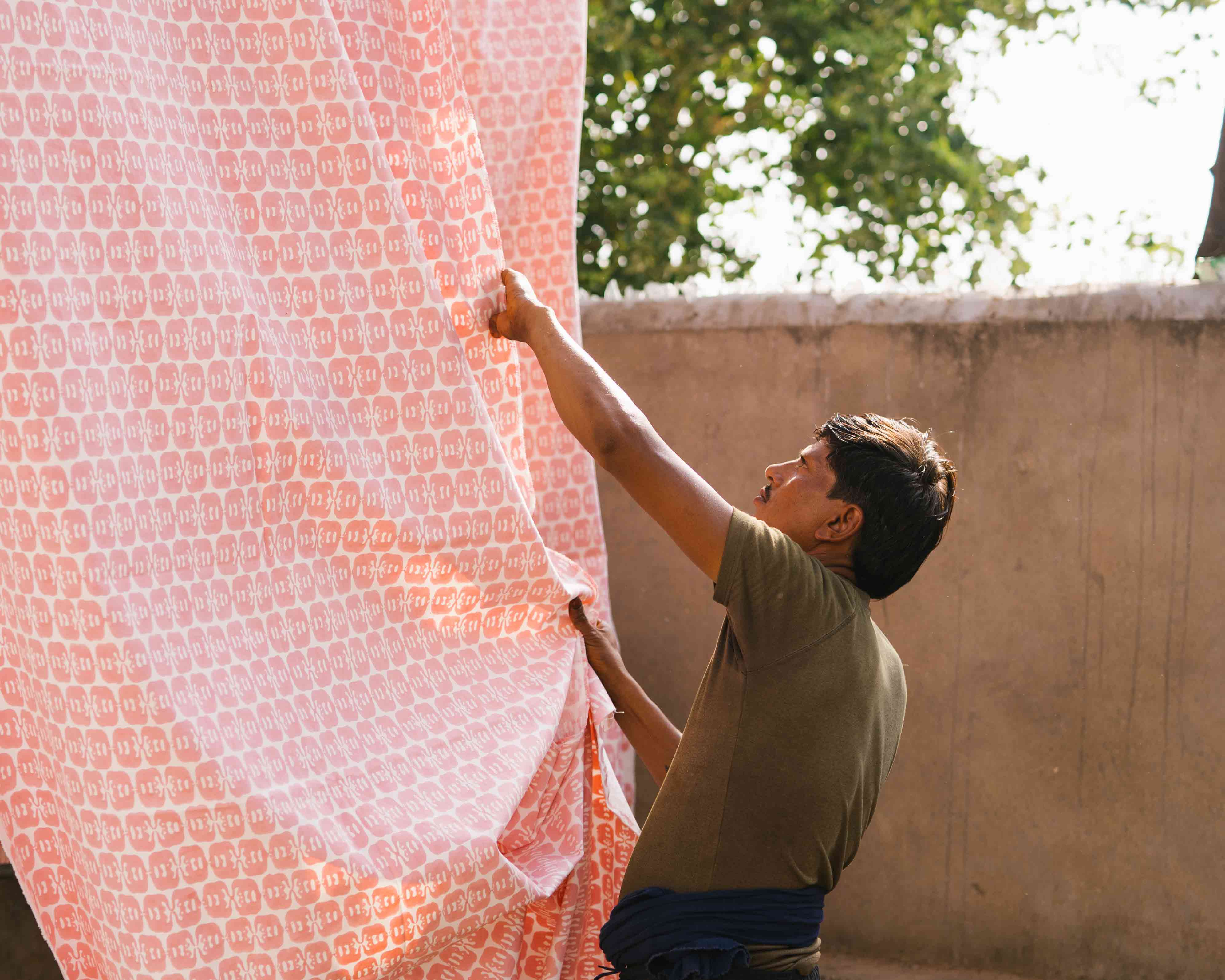
Step 5:
Our colour of choice is then rolled across our newly created blocks and our talented artists begin to hand-press the blocks onto the fabric to create beautiful patterns. This process is repeated again and again until the length of the fabric is complete. After all the hard work, the print is left to soak in, given a good wash and left to dry in the sun. And voila! We have our finished fabric.
Step 6
Now it's time to bring the pieces to life! Our talented seamsters meticulously cut the printed fabric into patterns and then expertly stitch together all the various parts.

Step 7
It’s now time to add the final details such as our signature Love Brand & Co. label and corozo nut buttons. And just like that, we have a finished block printed garment ready to wear on your next holiday adventure.
In a world dominated by machinery and mass production, we take pride in employing eco-friendly, handcrafted techniques and sustainable materials. To be able to continue such an ancient and culturally significant art form is an honour and we're excited to bring you along for the journey.
You can find our latest block printed clothing and accessories below, stay tuned for more updates!